Here's the story of "the making" of the EOV2000 system...
It was somewhere in 1998, a friend asked me to make her a steam distiller, just like the "classic" ones you see for sale on the internet here and there. So I built one just like this for her, basically copying classic textbook steam distillation designs similar to ones that my competitors currently use, except I used all glass and glass taper-joints instead of rubber hoses and stoppers:
The "classic-textbook" design goes like this;
You boil water in the left hand flask (photo below) and it creates steam.
The steam is piped into the bottom of the middle of the flask which holds the biomass™ or material to be steam distilled.
The vapors from that rise, go out the top, thru the angled condenser and to a catch-flask.
After the distillation is complete, the results are poured into a separatory funnel and the oil & water are allowed to separate,
then drained off into their respective containers.
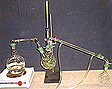
Click the photo for more pics
I decided that since I was making this for her I ought to test it first and make sure it all worked properly. So I filled the bioflask™ with Rosemary, fired it up, and a couple of hours later saw a tiny blob of oil floating on top of the catch-flask. I then used the standard routine of pouring all the condensed water and oil into a separatory funnel and letting it sit a while, then I drained all the water out and finally the two drops of oil that were in there. In the end, the bioflask™ was still 1/4 full of water, the room smelled horribly strongly of Rosemary, the process had taken forever, produced very little oil, and was entirely frustrating. I immediately thought to myself, "nope, this can't be the right way to do this".
So I embarked on a few months of trial and error, redesigning the system from the ground up.
I'd noticed in the first setup that the bioflask™ had condensed about 1/4 full of water by the time the run was over, and that was not good because it covered plant material rendering it undistillable, and wasted the boiling water. It (the bioflask™) also took forever to get hot.
So I decided the bioflask™ should sit right on top of the steam generator, so it could receive it's steam directly without messy hoses, and any condensing water would just flow back into the boiler and be reused. This would also keep all the plant material from being covered with water thus undistillable
So here was the next round:
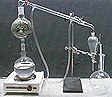
Click the photo for more pics
As you can see here, I also modified a separatory funnel with a side outlet and anti-siphon vent, so that it would constantly (and automatically) separate condensed water from the oil, allowing me to distill for much longer times without having to change the catch-flask, and more important, I wouldn't have to transfer the water/oil to a sep funnel once I was done- it is now already there!.
It was beginning to work extremely well!!
I obtained a LOT more oil this time, and the sep funnel modifications worked perfectly..
But I realized that the new sep funnl design should be small in diameter, so there wouldn't be such a big glass wall surface for "my precious" oil to stick to and be wasted on. But at this point I realized I was on the right track, because the yield was now in the neighborhood of 3-4 mL instead of 3-4 drops of the first attempt. !!!
The next trial was very funny... once I figured out that the bioflask™ should sit on top of the steam generator, I thought that it'd be neat to make a completly vertical system so it didn't take any counter space at all. So I created a 3 foot long vertical condenser that had a side-drain for the condensed liquids, and a top vent. It sat right on top of the bioflask™.
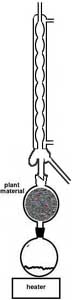
I loaded up the bioflask™ with a full charge of rosemary, turned it on and called my wife down to see it go for the first time, and...uh-oh... the entire batch of vaporized oil went straight up and out the top, and not a drop of it condensed!! Talk about having to learn to love Rosemary the hard way... I figure I let almost 4 mL of pure vaporized oil out into my workshop...oops... !!
Well, at least that experience taught me to like Rosemary, which until then I didn't... because I had to live with it smelling VERY strongly in my daily workspace for almost two months!!
The Final Design:
With that, I realized that since running the condenser straight up didn't do a thing, and that running it at the angle you see in the photos above worked "kinda" ok but a lot of vapor escaped, that the way to do it was run the condenser straight down.
This does three things:
(1), the unit gets small again and doesn't sprawl all over the kitchen counter;
(2), it minimizes the connections required- no more angles and bends necesary because the receiver™ can just hang on the bottom of the condenser;
(3), and most important, It creates the maximum turbulence inside the condenser making it extrememly efficient... steam wants to rise but I've now forced it to go down, so it gets agitated and much more of it hits the condenser walls in a smaller space. This means more oil gets caught and condensed and less escapes.
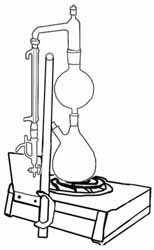
All in all a few more refinements and I arrived at what you see now on my main webpage.
It was a very fun development process, and since then, the feedback from customers has been especially rewarding!
...Gary Stadler